When planning a piping system, selecting the right HDPE (High-Density Polyethylene) pipe fittings is crucial to ensuring efficiency, durability, and long-term performance. HDPE pipe fittings offer excellent resistance to corrosion, chemicals, and extreme environmental conditions, making them the preferred choice for various industries, including water supply, agriculture, gas distribution, and industrial applications. However, choosing the right fittings requires understanding different factors such as types, applications, and installation methods.
In this guide, we will walk you through everything you need to know about selecting the right HDPE pipe fittings for your project.

Understanding HDPE Pipe Fittings
What Are HDPE Pipe Fittings?
HDPE pipe fittings are components used to connect, control, or alter the flow direction of HDPE piping systems. These fittings ensure leak-proof and efficient connections, enabling the pipes to handle high-pressure and demanding environments effectively.
Why Choose HDPE Pipe Fittings?
- Durability: HDPE fittings are resistant to corrosion, rust, and chemical exposure.
- Flexibility: They can handle high stress and pressure fluctuations.
- Leak Resistance: Heat-fused joints create a seamless system, reducing the risk of leaks.
- Longevity: HDPE fittings have a lifespan of over 50 years with minimal maintenance.
- Eco-Friendly: 100% recyclable and energy-efficient manufacturing process.
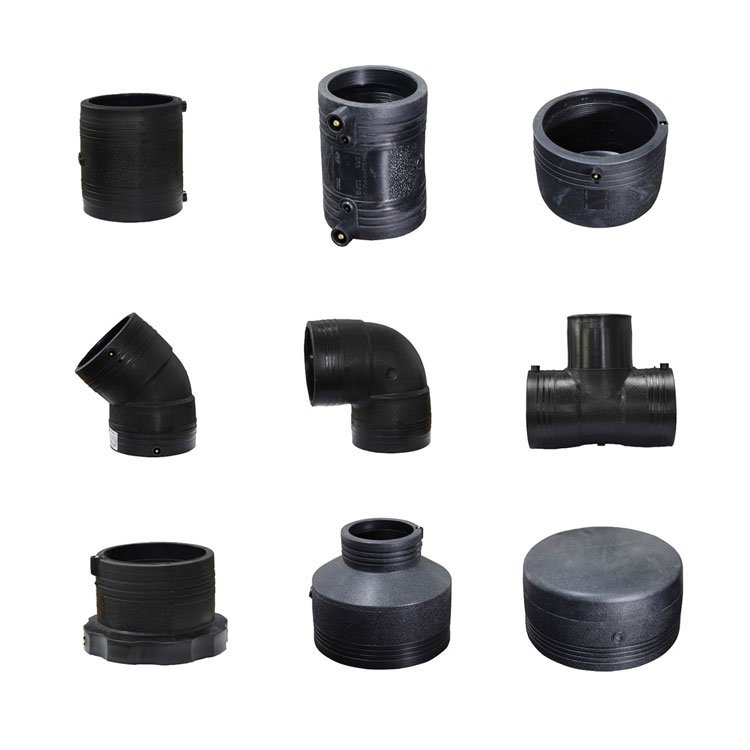
Types of HDPE Pipe Fittings
1. Couplings
Couplings are used to connect two HDPE pipes securely. They come in different types, including:
- Compression Couplings: Easy to install and commonly used in irrigation and plumbing.
- Electrofusion Couplings: Provide a strong, leak-proof bond using an electrical heating process.
2. Elbows
Elbows help change the direction of flow in the piping system. They are available in different angles such as 45-degree and 90-degree bends.
3. Tees & Cross Fittings
- Tees: Allow for branching of pipes in T-shaped junctions.
- Cross Fittings: Create four-way connections for complex piping systems.
4. Reducers
Reducers are used to connect pipes of different diameters. They help in controlling flow rates efficiently.
5. Flange Adapters & Stub Ends
Used for connecting HDPE pipes to other materials or components, such as valves or pumps.
6. Valves
Valves regulate flow within the system. Popular types include ball valves, gate valves, and check valves.
7. End Caps
End caps are used to close off the end of a pipeline to stop flow when needed.
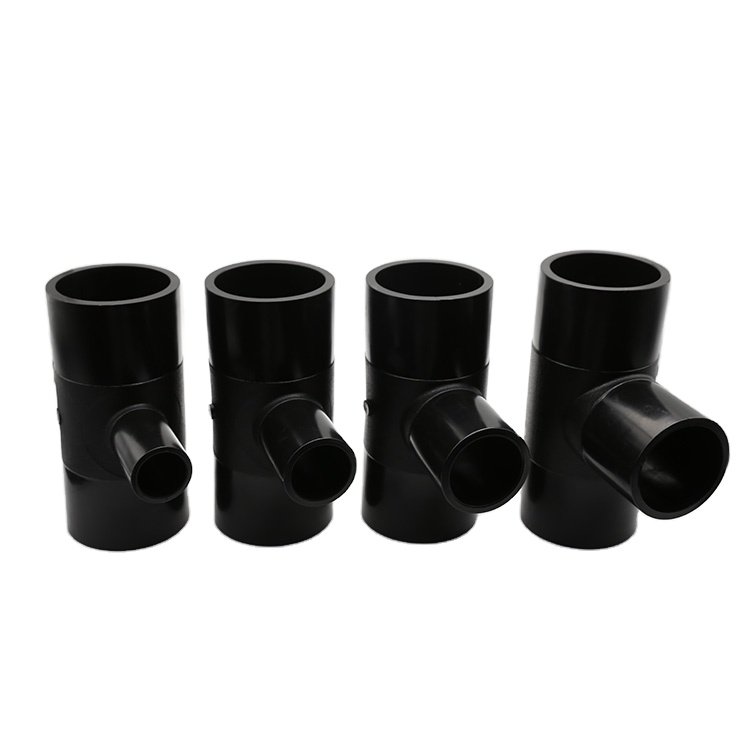
Factors to Consider When Choosing HDPE Pipe Fittings
1. Application & Industry Requirements
Different industries require different types of fittings. For instance:
- Water Supply & Irrigation: Requires leak-proof and corrosion-resistant fittings.
- Gas Distribution: Needs high-pressure-rated fittings.
- Chemical Processing: Requires fittings resistant to chemical exposure.
- Sewage & Drainage: Should handle high volumes of waste and water flow.
2. Pipe Size & Pressure Rating
Selecting fittings that match the diameter and pressure rating of your HDPE pipes ensures a secure connection and prevents system failures.
3. Jointing Method
HDPE fittings can be connected using different techniques:
- Electrofusion Welding: Uses an electric current to heat and fuse fittings, ensuring a strong connection.
- Butt Fusion Welding: Melts and joins pipe ends using pressure and heat.
- Compression Fittings: Require mechanical tightening, commonly used for temporary installations.
4. Environmental Conditions
Consider the external conditions where the system will be installed:
- Underground Installations: Require high-pressure fittings with durability.
- Harsh Chemical Environments: Need chemical-resistant fittings.
- Extreme Temperature Areas: Should use fittings that withstand expansion and contraction.
5. Compliance with Standards
Ensure that your HDPE fittings meet industry certifications such as ISO, ASTM, AWWA, and BIS to guarantee quality and performance.
Installation Best Practices
1. Proper Pipe Alignment
Before installation, ensure pipes are properly aligned to prevent stress on fittings and potential leaks.
2. Clean the Jointing Area
For electrofusion and butt fusion, clean the pipe ends thoroughly before welding to ensure a strong bond.
3. Follow Manufacturer Guidelines
Different fittings require specific installation techniques. Always follow the manufacturer’s guidelines for best results.
4. Use Proper Welding Equipment
For heat fusion methods, ensure you use high-quality welding machines and trained professionals for the job.
5. Conduct Pressure Testing
Once the fittings are installed, conduct a pressure test to verify that the system is secure and free from leaks.
Benefits of Choosing the Right HDPE Pipe Fittings
By selecting the right fittings for your project, you can:
- Enhance system efficiency with optimized flow control.
- Prevent leaks and damage, reducing maintenance costs.
- Increase the lifespan of the piping system, ensuring long-term durability.
- Ensure regulatory compliance with industry standards.
Conclusion
Choosing the right HDPE pipe fittings is essential for ensuring the success of your project. By considering factors such as application type, pipe size, jointing method, environmental conditions, and compliance standards, you can make an informed decision and optimize your piping system’s performance.
At Petron Thermoplast, we offer a wide range of high-quality HDPE pipe fittings for various industries, ensuring durability, strength, and leak-proof performance.
Leave a Reply