Aluminum fabrication work plays a pivotal role in the development of modern architecture, infrastructure, and manufacturing. From sleek building facades to custom-designed interior fixtures, aluminum fabrication enables designers, engineers, and contractors to push the boundaries of creativity and functionality. If you are looking to achieve exceptional outcomes in your next construction or design project, understanding the potential of aluminum fabrication is essential.
In this article, we will explore how aluminum fabrication can deliver stunning results, its advantages, popular applications, techniques involved, and what to consider when selecting a fabrication partner.
Note: Aluminum Fabrication Work was successfully executed by skilled experts, delivering high-precision structures with lasting strength and appeal. From design to installation, every step reflected craftsmanship and innovation. Trust your next project to
Aluminium Scaffolding Fence
for superior results in aluminum solutions. Contact us today for customized fabrication excellence.
Understanding Aluminum Fabrication Work
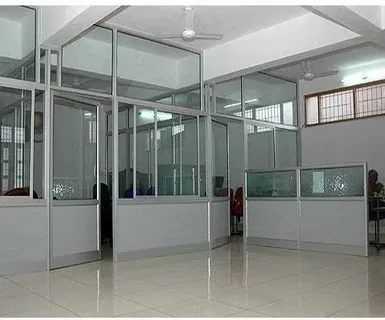
Aluminum fabrication refers to the process of cutting, bending, welding, and assembling aluminum materials into specific shapes or products. Aluminum is one of the most versatile and widely used metals, prized for its lightweight nature, corrosion resistance, strength, and excellent workability.
Fabrication may involve sheet metal work, structural frameworks, cladding systems, or custom installations. From curtain walls in skyscrapers to decorative panels and partitions, aluminum fabrication supports a diverse range of industries including construction, automotive, aerospace, marine, and signage.
Why Aluminum Is the Ideal Material for Modern Fabrication
Aluminum’s popularity in fabrication is not by chance. Several inherent characteristics make it highly preferred across both functional and aesthetic applications:
Lightweight yet strong
Aluminum offers the best of both worlds: it is approximately one-third the weight of steel while still providing high tensile strength, which makes it easier to handle, install, and transport.
Corrosion resistant
Its natural oxide coating protects aluminum from rust and environmental damage, making it ideal for outdoor use and coastal applications.
Malleable and flexible
Aluminum can be easily cut, bent, and welded into intricate shapes without cracking. This allows for more complex, customized designs to be fabricated with precision.
Sustainable and recyclable
Aluminum is 100% recyclable without loss of quality. Utilizing recycled aluminum also significantly reduces energy consumption, making it an eco-conscious choice.
Common Applications of Aluminum Fabrication
The scope of aluminum fabrication is broad, and its adaptability allows it to be used in multiple sectors:
Architectural and construction
Aluminum is used in the production of structural frameworks, wall cladding, roofing systems, louvers, handrails, and more. Curtain walls and windows in commercial buildings are often fabricated from aluminum for their lightweight nature and weather resistance.
Interior design and partitions
Aluminum fabricated elements such as doors, sliding systems, partition walls, ceilings, and furniture provide a modern, clean finish that blends well in residential and office environments.
Automotive and transport
The transportation sector uses aluminum for car frames, railway systems, aircraft components, and marine vessels due to its weight savings and durability.
Industrial equipment and machinery
Fabricated aluminum is used in the creation of machine enclosures, control panels, frames, and other custom industrial parts where strength and corrosion resistance are essential.
Signage and displays
Custom fabricated aluminum panels are widely used in the retail and advertising industries for signs, display stands, and exhibition booths.
Techniques Used in Aluminum Fabrication Work
Achieving stunning results requires the correct fabrication techniques and high-quality materials. Here are some of the most common aluminum fabrication processes:
Cutting
Laser cutting, water jet cutting, and plasma cutting are used to shape aluminum sheets or profiles with high precision.
Bending and forming
Aluminum can be bent into various angles using press brakes or rolling machines. The process must be carefully controlled to prevent cracking or warping.
Welding
TIG (Tungsten Inert Gas) welding is the preferred method for aluminum. Skilled welders ensure clean joints without compromising strength or aesthetics.
Machining
CNC machining enables the shaping of complex components with tight tolerances, ensuring accuracy in high-performance applications.
Finishing
Anodizing, powder coating, or painting are used to enhance the appearance and durability of aluminum surfaces. These finishes also offer a wide range of colors and textures.
Design Flexibility and Aesthetic Possibilities
Aluminum fabrication opens the door to limitless design potential. Its adaptability allows designers to incorporate sleek curves, intricate patterns, or minimalist structures without compromising on stability. Additionally, finishes such as brushed, mirror-polished, or matte powder coating allow for personalization to suit any architectural or branding style.
Whether you’re aiming for a modern industrial look or a sleek contemporary finish, aluminum can be tailored to meet your exact visual and functional needs.
Enhancing Energy Efficiency and Sustainability
Aluminum is a champion of energy efficiency and sustainability. Its thermal conductivity can be harnessed or mitigated with insulated systems to reduce heat transfer. This makes it a valuable component in green building design. Furthermore, by selecting recycled aluminum and eco-friendly finishes, your project’s carbon footprint can be significantly reduced.
Factors That Influence the Quality of Fabrication
Unlocking the full potential of aluminum fabrication work depends on several key factors:
Quality of raw materials
Using high-grade aluminum alloy ensures the strength, longevity, and finish of the final product.
Expertise of the fabricator
Skilled technicians and engineers with experience in aluminum fabrication can ensure precision, safety, and aesthetic excellence.
Equipment and technology
Modern fabrication workshops with CNC machinery, laser cutters, and advanced welding tools can achieve more intricate and accurate results.
Design and engineering support
Collaborating with a fabricator who offers in-house design and technical support can streamline the fabrication process and improve outcomes.
Choosing the Right Aluminum Fabrication Partner
To achieve outstanding results, it’s essential to choose the right aluminum fabrication company. Look for:
- Proven experience and portfolio in similar projects
- Ability to handle custom designs and large-scale production
- Transparent pricing and detailed quotations
- Certifications for quality and safety compliance
- Strong communication and project management capabilities
A reliable partner will not only deliver a well-fabricated product but also provide valuable guidance throughout the design and execution phases.
Case Studies and Real-World Applications
Aluminum fabrication has helped transform iconic buildings, efficient workspaces, and futuristic product designs worldwide. Projects that incorporated innovative aluminum structures have seen increased durability, aesthetic appeal, and lower long-term maintenance costs.
For instance, modern corporate offices with aluminum partition systems reported improved workspace flexibility and acoustic control. In another example, large-scale signage made from fabricated aluminum offered a lightweight yet durable solution for outdoor branding in extreme weather conditions.
Maintenance and Longevity of Fabricated Aluminum Structures
One of the biggest advantages of aluminum fabrication is minimal maintenance. Aluminum naturally resists rust, pests, and UV damage. Occasional cleaning and routine inspections are usually enough to keep installations in optimal condition.
Powder-coated or anodized finishes further extend the lifespan of aluminum products by adding an additional protective layer, maintaining their original look for years.
Conclusion
Aluminum fabrication work offers a compelling mix of durability, flexibility, and visual appeal. Whether you are designing an architectural masterpiece, building a modern office space, or developing industrial solutions, aluminum can help bring your vision to life with style and efficiency.
The key to unlocking stunning results lies in choosing the right materials, techniques, and fabrication partner. With proper planning, professional guidance, and a clear vision, aluminum fabrication becomes a gateway to sophisticated, functional, and sustainable results.
For more insightful articles related to this topic, feel free to visit techners.net
Leave a Reply